本文目录导读:
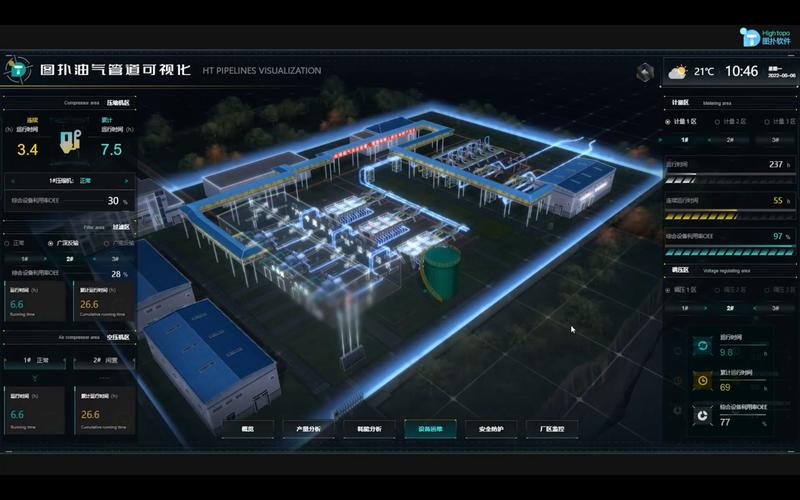
在当今数字化飞速发展的时代,数字孪生技术正以前所未有的影响力改变着我们生活的方方面面,它如同一面神奇的镜子,将现实世界中的物理实体完美映射到虚拟空间,创造出一个与之紧密相连、实时互动的数字“克隆体”,这一技术的出现,不仅为工业制造、城市管理等领域带来了革命性的变革,更为我们探索未知世界、优化决策过程提供了全新的视角和强大的工具。
数字孪生的起源与发展脉络
数字孪生的概念最早可追溯至 2003 年美国密歇根大学 Grieves 教授在产品全生命周期管理课程中提出的“镜像空间模型”,当时主要用于对产品状态的仿真模拟与预测,此后,随着技术的不断演进,其定义逐渐丰富和完善,2010 年,美国空军研究实验室正式提出机身数字孪体概念,并将其应用于飞机结构寿命预测等方面,而真正让数字孪生走进大众视野的是 2012 年美国国家航空航天局(NASA)发布的“全球科技愿景”报告,该报告指出数字孪生是驱动未来飞行器发展的关键技术之一。
从最初的军事及航空航天领域,数字孪生技术开始向其他行业拓展,在汽车制造领域,特斯拉等企业率先引入数字孪生技术构建工厂的数字孪生模型,实现了对生产过程的全面监控与优化;在建筑行业,通过创建建筑信息模型(BIM)的数字孪生体,可以在施工前进行性能模拟与优化,提高建筑质量与可持续性,如今,数字孪生技术已广泛应用于智能制造、智慧城市、医疗健康、交通运输等多个关键领域,成为推动各行业数字化转型的核心动力之一。
数字孪生的核心特征剖析
(一)模型支撑:贯穿全生命周期的精准表达
数字孪生系统依赖于模型来支撑其运行与应用,这些模型具有独特而关键的特性,其具备全生命周期贯穿性,从物理实体的设计阶段便开始构建数字模型,并伴随实体的成长、老化直至报废的整个过程持续演进与更新,在产品设计阶段,设计师可以根据数字孪生模型进行虚拟测试与验证,及时发现设计缺陷并进行优化,大大缩短产品研发周期、降低成本。
数字孪生模型呈现全方位表达的特点,不仅仅局限于产品的几何形状建模,还涵盖了工艺优化、制造过程规划、服务运维以及回收处置等各个环节的建模与仿真,通过建立如此全面的数字档案,能够实现对物理实体极为细致、精确且忠实的数字化呈现,以汽车发动机为例,其数字孪生模型不仅包含了发动机缸体、活塞等零部件的几何尺寸与结构,还模拟了燃料燃烧过程、气流运动规律以及各部件之间的摩擦与磨损情况等复杂物理过程,为发动机的性能分析与故障诊断提供了有力支持。
模型融合了多学科领域的知识与技术,现实中的物理系统往往涉及机械、电子、液压、气动等多个学科,因此数字孪生体的模型必须综合多领域、多学科的物理和管理模型,以实现对物理实体全面而准确的描述与分析,这种多学科融合的特性使得数字孪生技术在复杂系统的建模与优化方面具有独特的优势,如在航空航天飞行器的设计与研发中,需要综合考虑空气动力学、材料力学、飞行控制等多个学科领域的知识,数字孪生模型则能够将这些不同学科的知识有机整合,为飞行器的整体性能提升提供重要支撑。
(二)数据驱动:实时动态的智慧引擎
数据是数字孪生技术的核心基础与关键驱动力,来自物理实体及其周边环境的实时数据源源不断地输入系统,包括传感器采集的温度、压力、位置、速度等各种参数,以及设备运行过程中产生的振动、噪声等信息,通过对物理实体的虚拟模型进行模拟运算所获得的结果数据也是重要的组成部分,这些海量、多种类的数据通过先进的数据处理算法和分析技术进行处理与融合,形成有价值的信息,进而驱动数字孪生系统的运转与优化。
基于数据的智能感知与互联互通特性使物理实体与数字模型之间形成了高效、实时的交互机制,物理实体上的各种传感器如同敏锐的触角,实时感知周围环境变化并将数据传输给数字模型,数字模型则根据这些数据进行分析计算,及时反馈控制指令给物理实体,实现对实体运行状态的动态调整与优化,例如在智能工厂中,生产设备上安装的传感器将实时工况数据传输给数字孪生模型,模型根据数据分析结果自动调整生产参数,如机床的切削速度、进给量等,以保证产品质量的稳定性和生产效率的最大化,这种智能感知与互联的能力也为远程监控与协同工作提供了可能,操作人员可以通过网络随时随地获取设备或系统的运行信息,并进行远程操作与维护,极大地提高了生产管理的便捷性与灵活性。
为了确保数据的有效性和一致性,数字孪生系统采用了基于模型的数据管理方式,所有数据都通过信息模型、物理模型、管理模型等多个领域模型进行组织与管理,并通过统一的单一数据源进行存储与分发,这种严谨的数据管理模式保证了在整个数字孪生生态系统中,各个子系统和模块都能够访问到准确、可靠且一致的数据,从而为实现系统间的协同工作与整体优化奠定了坚实基础,例如在一个大型城市的交通管理系统中,交通流量监测数据、道路设施信息、车辆行驶数据等都通过统一的数据管理平台进行整合与分析,为交通信号灯的智能调控、公交线路的优化调整以及交通事故的快速处理提供了有力的数据支持,有效提升了城市交通的运行效率与管理水平。
(三)实时映射:虚实交互的无缝对接
数字孪生系统最为显著的特点之一便是其能够实现物理系统与数字模型之间的实时连接与动态交互,这种双向映射关系确保了物理实体的任何细微变化都能实时反映在数字模型中,反之亦然,当物理系统中的设备发生故障、性能出现波动或者外部环境发生改变时,数字模型会立即捕捉到这些变化并在虚拟空间中进行相应的呈现与分析,例如在能源管理系统中,当电网负荷突然增加时,数字孪生模型能够迅速感知到电力供应的变化,并通过模拟计算预测可能出现的问题以及对整个能源供应网络的影响,及时为调度人员提供决策支持,以便采取相应的措施进行调整,保障能源供应的稳定与安全。
与此同时,数字模型的仿真结果也能够实时反馈给物理实体,对其运行过程进行指导与控制,通过对物理实体未来行为的预测与推演,数字孪生系统可以提前制定优化策略并下发控制指令,使物理实体按照预定的目标和最优的路径运行,在工业生产线上,数字孪生模型可以根据订单需求和原材料供应情况预测生产进度和质量状况,并实时调整设备的运行参数和工艺流程,确保生产过程高效、稳定地进行,这种虚实融合的特性打破了传统物理系统与信息系统之间的壁垒,使两者形成一个有机的整体,共同协作实现系统的功能与目标,极大地提升了系统的响应速度、适应性和可靠性。
(四)适合应用场景的实时连接:灵活适配的定制化服务
数字孪生技术的应用范围极为广泛,但在不同领域中其对实时性的要求却有所差异,在控制类应用场景中,如自动化工厂生产线的监控与控制、无人机的飞行操控等,通常需要极高的实时性,要求系统能够在毫秒级别甚至微秒级别内做出响应,这是因为在这些场景下,任何微小的延迟都可能导致严重的安全事故或质量问题,在高速自动化装配线上,机器人的操作需要与传送带的运动、物料的供给以及产品的质量检测等环节紧密配合,实时连接的延迟必须控制在极小范围内,才能保证生产的连续性和产品的准确性。
对于生产系统级应用场景,如化工生产过程的监控与管理、钢铁冶炼流程的控制等,虽然对实时性的要求相对较高,但一般可以接受小于 10 秒甚至 1 分钟的延迟,这是因为在这些大规模生产过程中,物理过程本身具有一定的惯性和缓冲能力,短暂的数据延迟不会立即导致严重后果,但仍需及时准确的数据支持来进行有效的控制与优化,例如在化工反应釜的控制中,温度、压力、浓度等参数的变化相对较为缓慢,即使数据更新存在一定的延迟,只要在合理范围内,仍可通过控制算法进行有效的调节,避免事故发生并确保产品质量稳定。
在大系统应用场景中,如城市级别的交通管理、水资源调配等,某些数据更新频率较低,可能以分钟甚至小时为单位进行更新,这并不意味着对实时性的忽视,而是根据系统的规模和特点进行了合理的权衡,城市交通流量的变化是一个相对缓慢的过程,在几分钟甚至更长时间内的交通数据仍然具有参考价值,通过对这些数据的分析和预测,可以提前制定交通疏导方案,缓解交通拥堵,同样,在水资源调配方面,河流水位、水库蓄水量等数据的变化也较为平缓,以小时为单位更新的数据足以支撑水资源管理部门做出科学合理的决策,如灌溉计划的制定、水电站发电量的调节以及防洪预警等,无论是哪种类型的应用场景,“实时连接”的本质都是确保虚拟和现实的系统集成和协同工作,使数字孪生系统能够真正发挥其应有的作用,为实际生产和生活提供有效的支持与服务。
(五)智能决策:预见未来的智慧大脑
数字孪生技术的核心价值之一在于其强大的智能决策能力,通过将物理实体的实际运行状态与高精度的数字模型相结合,在软件界面中直观地呈现出系统的各种信息,实现对物理实体的实时监控与智能分析,在监控系统中,不仅能够实时显示物理实体的各项实时数据,还能通过数据分析算法提取出有价值的信息,如设备的健康状态、生产过程中的潜在风险、能源消耗情况等,例如在风力发电场中,数字孪生系统可以实时展示每台风机的转速、功率输出、叶片角度以及所处环境的风速、